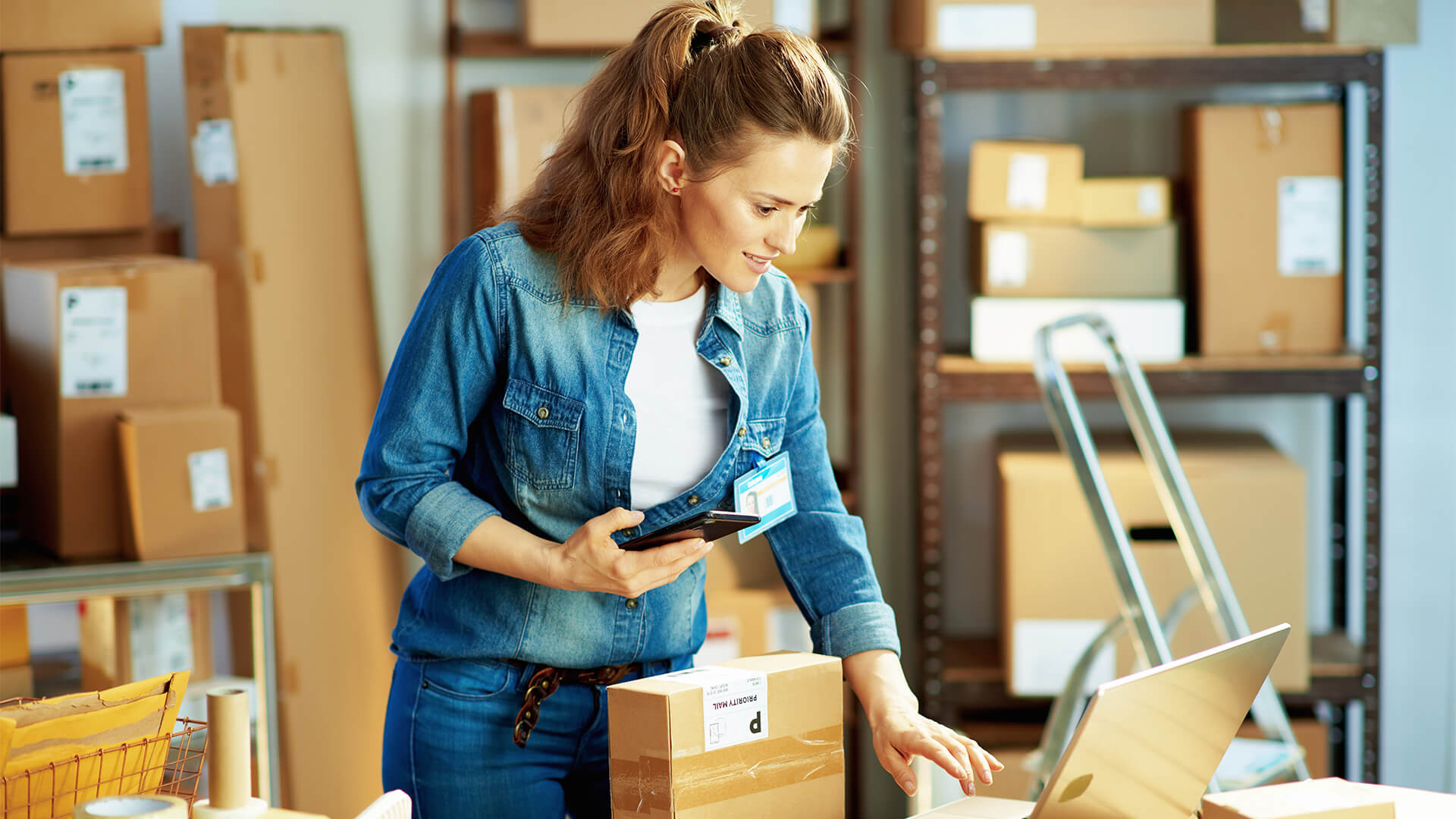
All business processes can be stressful, from product development to order fulfillment. Sadly, this stress doesn’t lessen once your product has reached the packaging process, especially if your business deals with the distribution of fragile products. Devising innovative ways to prepare fragile products for shipping can be highly burdensome, as the last thing you’d want to happen is for the product to reach its destination in a state of disrepair.
Luckily for businesses, there are various ways that fragile objects can be packaged and prepared for dispatch, from making simple choices like choosing sensibly sized packaging and using enough wrapping materials to using helpful packing tools such as a case packer or a gravity case. This article outlines a few tips for shipping fragile products for your business so that the process of shipping both domestically and overseas is much more straightforward and less stress-inducing.
Don’t Skimp On Wrapping Materials
Wrapping materials are handy for businesses that package and prepare fragile products for overseas and domestic shipping. However, wrapping materials are only helpful if an adequate amount has been used; if your business skimps on the amount of wrapping material used per product, then this could lead to breakages during transit and, worst-case scenario, unhappy customers.
Therefore, make sure that a generous amount of bubble wrap or a similar wrapping material is used, especially if the product being prepared for dispatch is glassware or is hugely at risk of breaking during transit. As an added security measure, you could even use packing peanuts to fill the gaps between the product and the container it’s been packaged in as well as using protective wrapping material around the product itself.
Make Sure Items Are Wrapped Properly
Using enough wrapping materials for fragile products is one thing. Still, protective wrapping is useless if it hasn’t been applied correctly or is likely to fall off or loosen in transit. To avoid this, you’ll probably need to use tape or zip-lock bags to secure your protective wrapping of choice around the product to ascertain that it won’t fall off or loosen once it’s left your warehouse.
On the other hand, you could take your packaging process to the next level by considering automating it. Consider enlisting the services of companies such as BluePrint Automation and their innovative automatic case packing and tray packing solutions to help your business optimize your product handling and packaging processes.
Contact a team member today to start devising a solution for your packaging needs and learn more about BPA’s gravity case solutions, which will undoubtedly help take your business packaging processes to the next level.
Label Your Packing
Once your product has left your warehouse, the security of that item lies within the hands of your chosen courier. Therefore, if the packaging hasn’t been clearly labeled as fragile, the courier will be none the wiser and could treat it as a regular, non-fragile package.
Your business can make identifying fragile packages easier for the people handling them by labeling them as fragile on every side of the box and putting a ‘this way-up’ sticker on top. This way, it’s clear that the package is delicate, and any breakages will be their fault.
Seal the Box
Once your product has gone through all stages of the packaging process, you are now ready to distribute it to its destination by carrying out all final checks and sealing the box once you are satisfied. Much like wrapping materials, we recommend that you don’t skimp on the amount of tape you use either, as you wouldn’t want this to loosen or fall off in transit either. Invest in strong, high-quality packing tape and try to seal any visible gaps to minimize the risk of the box accidentally opening during the shipping process and keep your customers happy.